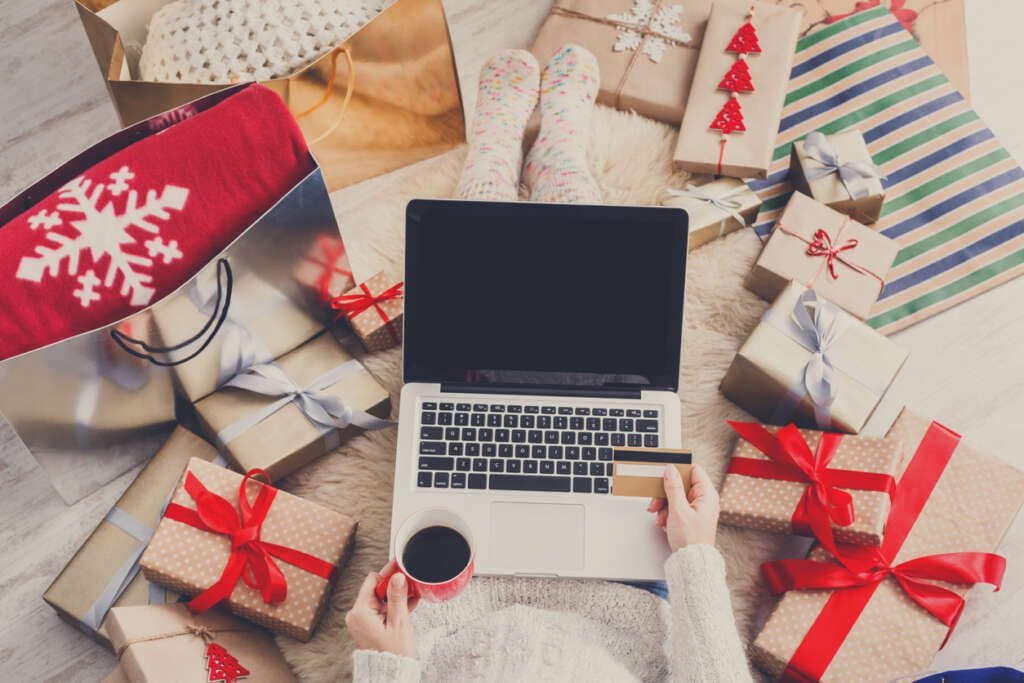
As we head into autumn, retailers are gearing up for the manic weeks of Christmas peak 2022. Things will very likely kick off on Black Friday – Friday 25th November this year – so recruiting warehouse staff and meticulously planning the fulfilment and delivery of online orders is carried out as early as possible. This is particularly the case for e-commerce players who send large volumes of parcels to shoppers all over the world.
Customers whose toys, gifts and party dresses fail to arrive in time for Christmas can be very unforgiving. So, understandably, no-one in retail wants to read stories about lack of progress in “delivering efficiencies”[1], or customers still waiting for Christmas items from December 2021[2]! There are certainly challenges ahead this year, with Brexit still slowing down cross-border shipments, and strikes and staff shortages hampering some parcel shipping routes. What can be done to smooth the process of cross-border e-commerce deliveries, and save retailers from the almighty seasonal headache of delayed deliveries?
Technology to the rescue
It can’t solve everything, but many in the industry are turning to automation to ease their pain. In the next few years, automated processes in fulfilment centres and warehouses will need to massively scale up, so that retailers can keep pace with customer demand for fast, reliable receipt of their parcels and packages, and overcome the pinch point of peak.
With the e-commerce market at an all-time high, brands and their supply chain partners are looking to adopt automation and robotic technology in their operations and processes to minimise errors, increase inventory accuracy, overcome labour shortages, and improve worker safety. All of these changes will inevitably lead to higher productivity and profit levels and increase effectiveness when it comes to warehouse management, and e-commerce fulfilment. According to a post-pandemic study[3], the warehouse automation market will reach the milestone of US $30 billion by 2026, at a CAGR of 14% between 2020 and 2026.
There’s plenty of evidence in the market to show how robotic technology can streamline processes in the e-commerce warehouse, while boosting customer service levels. We hear a lot about innovation using AI, data analytics and machine learning to drive efficiency. There are countless AR and VR developments coming through too, however these seem not to be taking off as dramatically as was envisaged a couple of years ago.
For me, operational automation is the tech that will give retailers – and the logistics partners they rely upon so heavily – competitive edge in the coming decade. For example, at Asendia UK we have just implemented six robotic arms capable of over-labelling 7,200 parcels an hour, which will vastly speed up a very manual process and free up operational colleagues for other tasks. The robots are coupled with an automated parcel sorter that will scan, weigh and sort the parcels to all global locations.
Managing the seasonal rush
As e-commerce has grown exponentially, there can be challenges in warehouses when manual work becomes too challenging, due to the sheer volume of parcels that need to be processed. For example, Black Friday inevitably results in a surge in parcels being posted out to customers. GlobalData[4] analysts estimated that UK shoppers spent around £9.2bn over Black Friday weekend in November 2021 – 15% more than in 2020. Such seasonal shopping bonanzas create huge spikes in demand for services at e-commerce fulfilment and distribution sites.
With automation comes the ability to scale volumes, offer flexible services, provide useful data, and release employees from difficult, manual work. Retailers, many of whom have fast-growing e-commerce audiences around the world, want to benefit directly from seeing their parcels pass through facilities faster than ever. There are also labour cost efficiencies in the long-term.
By introducing different robotic and automated solutions it’s possible to rationalise storage space, as well as accelerate the lead time between customers ordering and receiving their goods. You’re introducing smoother, safer operations overall too, often with a more logical flow of parcels through the building.
Agility and flexibility are key
When committing to warehouse automation, specialist logistics companies must be reactive and able to offer flexibility in fulfilment needs.
A major challenge with parcel processing automation is designing and developing robotic functionality that can handle a plethora of different sized boxes and bags, as well as mixed sizes of pallets, boxes and containers where the parcels are placed ready for shipping. This is particularly the case with warehouses processing parcels from many different retailers and brands, all of which will have different packaging, labels, sizing and customer care needs.
Data systems also need to integrate, both with the retail client, and with a host of shipping partners, in our case air freight companies for onward transportation.
If you can embed reliable technology that supports all these anomalies, it’s possible to meet the needs of retail sellers, and help them hit growth and speed-of-delivery targets.
Don’t spoil Christmas
Throughout the retail supply chain, robotic technology is helping to take the strain, especially during seasonal peaks when customer satisfaction can be put at extreme risk. A slicker business model lets firms and individuals send and receive items confidently. With Christmas fast approaching, I think many customers will be holding their breath that things will be delivered promptly. An up-to-date automated system helps massively with that precious task.
[1] https://news.sky.com/story/royal-mail-losing-1m-a-day-chairman-says-12655417
[2] https://www.gazetteandherald.co.uk/news/20584591.im-still-waiting-christmas-cards—said-postal-delays/
[3] https://forwardermagazine.com/warehouse-automation-market-post-covid-19-opportunities-worth-30b-by-2026
[4] https://www.theguardian.com/business/2021/nov/20/black-friday-uk-john-lewis-asda-currys-deals-shortages